Oxford Thermofluids Institute | Research - Research Groups: Active Flow Control Group

Active Flow Control Group
The Active Flow Control Group specialises in the development of novel technologies for controlling fluids, with a focus on cutting-edge aerospace applications. Led by Dr Marko Bacic, the group operates at the intersection between control engineering and fluid dynamics, and its research activities span the full gamut from fundamental physics to the development of industrially relevant devices ready for use in applications. The Active Flow Control group works very closely with Rolls-Royce plc. Much of the group’s research is funded by the UK government through InnovateUK and the Aerospace Technologies Institute.
Applied research conducted by the group supports a number of different overarching enterprises. The current primary applications include supporting the development of zero-carbon, hydrogen-fuelled jet engines; solving problems relating to eVTOL (Electric Vertical Take-Off and Landing) aircraft for enhanced urban mobility; and the design of modulated air systems to enhance the efficiency of conventional fuel civil aviation turbofan engines.
Complementing these endeavours, the Active Flow Control Group also performs fundamental research into the underlying physical mechanisms, enabling deep understanding of the principles to be developed. Of particular interest is the response of jets to acoustic- and ultrasonic actuation and the control of separated flows.
Numerical simulation of acoustic jet response
Fluidics
The Active Flow Control Group is at the forefront of world-class research in the field of fluidics, enabling the design of practical, no-moving-parts devices that can operate in the harshest environment with minimal maintenance requirements.
Under the PINES (Powerplant Integration of Novel Engine Systems) project, the group has developed a modulated air system based around a fluidic Switched Vortex Valve (SVV) that permits the turbine cooling air flow to be reduced during cruise. This increases the overall cycle efficiency of the engine, helping to reduce fuel burn and the environmental impact of civil air transport. The modulated air system has no mechanical moving parts and can be controlled either by using a sound input from piezo-electric transducers or by plasma actuation from sparks.
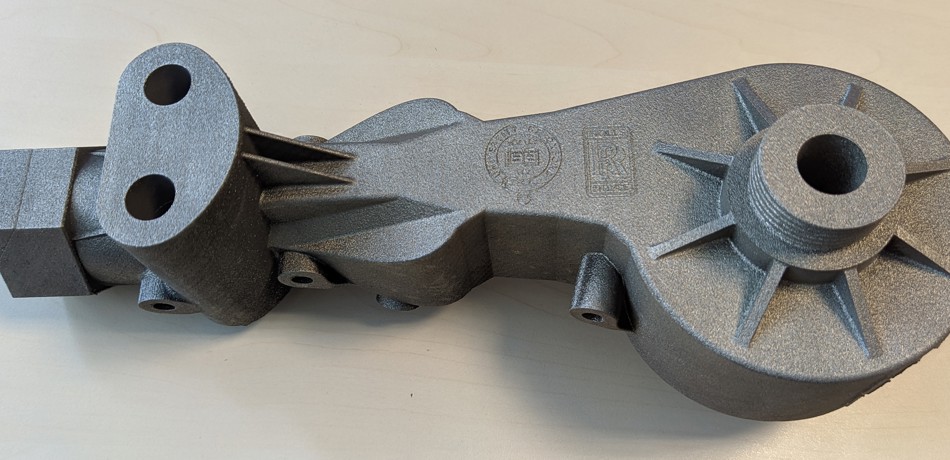
Prototype fluidic Modulated Air System device developed under PINES
The understanding gained from this development is now being taken forward under the LH2GT (Liquid Hydrogen for Gas Turbines) project. In this project, the Active Flow Control group is applying its fluidics expertise to the problem of metering and control of the fuel flow to the burner for liquid hydrogen-fuelled jet engines. This is vital for zero-carbon emission aviation to become a reality.
Former DPhil Students
Dr Mark Potter, 2008. “Non-Return Valve Instabilities”
Dr Andrew van Paridon, 2016. “Thermal modelling and control of high pressure turbine subsystems”
Dr Michael Mair, 2019. “On dynamics of fluidic jet switching and shear layer instabilities”
Dr Chris Nicholls, 2021. “The analysis, modelling, and acoustic control of fluidic devices”
Dr Patrick Boyle, 2022. “Development of a diverter piloted switched vortex valve for secondary flow modulation”